Rocket Science
In this project a composite rocket was analyzed which uses water and pressurized air as propellant. The investigation involves the outer flow around the rocket and also the internal flow in the rocket chamber. The rocket is 2,2 m high, has an outer diameter of approximately 10 cm with a dry mass of 1650 g. It was built/reinforced mainly from carbon fiber composite. The inner volume of the rocket is almost 13l which can be filled up to max. 25 bar pressure.
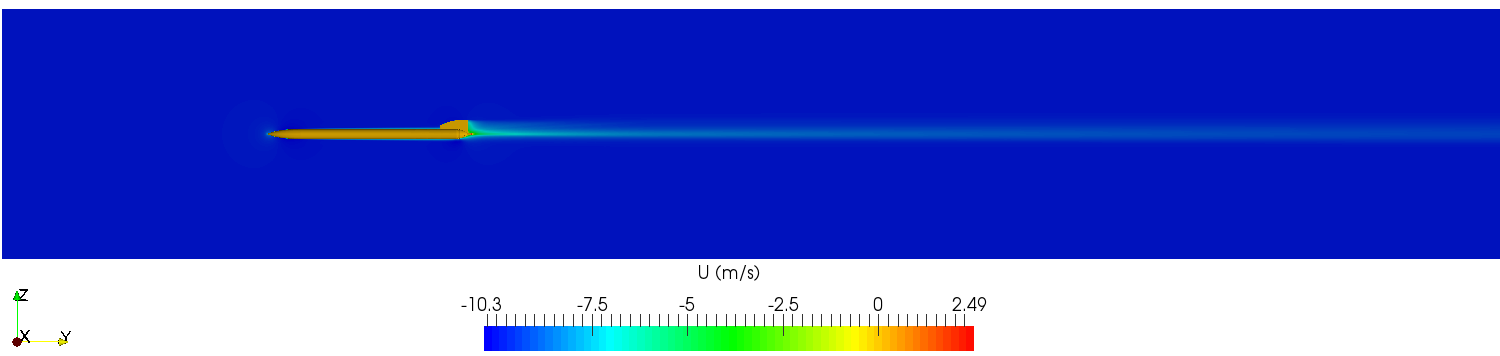
Velocity profile of the whole simulated domain.
The goal of the investigation is to calculate the rockets maximum altitude using CFD, considering the air resistance and the partially multiphase, high velocity outflow at the Laval nozzle. Therefore, the case was split up into two separate computations. Single phase outer flow around the rocket for the drag coefficient calculation and a multiphase simulation of the outflow to calculate the thrust at the Laval nozzle.
Mainly these two simulations combined with the rocket equation were used to calculate the maximum altitude. The results of the computation can be also used to understand in detail the interaction of water and air in the rocket chamber during the outflow. The initial conditions for the calculation were 3l of filled soapy water and 17 bar pressurized air. The outflow can be basically split up into three main stages. Clear, single phase water outflow, multiphase outflow of water and air, nearly clear air outflow where the Laval nozzle comes principally into effect.
For the computation the open source program OpenFOAM was used using VoF method and LES turbulent model. As a validation video recordings about the lift off and the flying of the rocket were used and also analytical and numerical calculations were achieved at the cross section of the Laval nozzle for the whole flight as controlling reasons. According to the calculation with the presented initial conditions the rocket reaches a maximum altitude of 154 m. The rocket is equipped also with an accelero- altimeter. As further validation with the measurement flights (planned in the soon future) the computed functions of the outflow will be comparable with the reality.
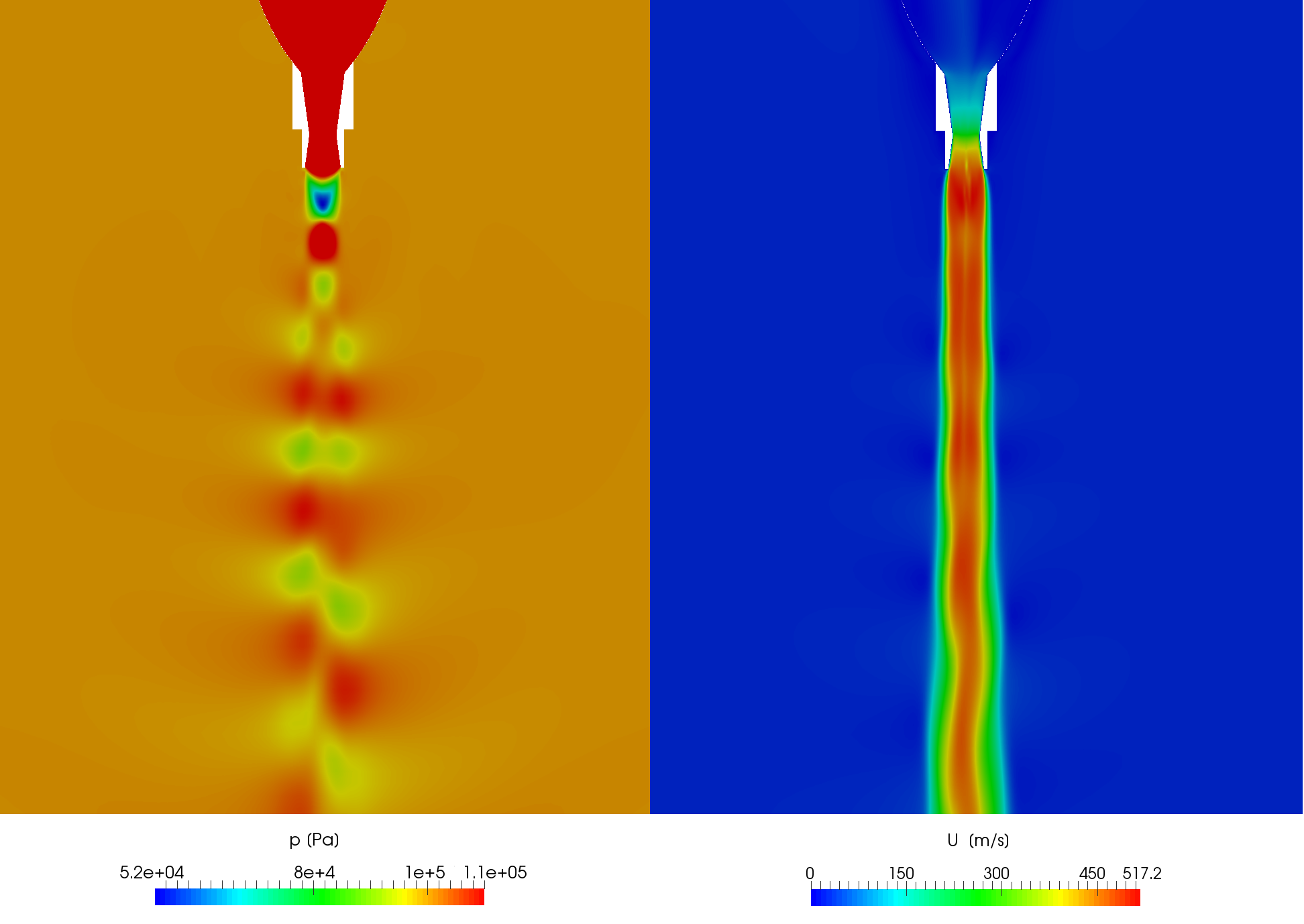
Pressure and velocity profile at the nozzle exit.